How much is time costing you?
- Fleet Harmony Inc
- Dec 29, 2021
- 3 min read
If time costs money and time is a measure of success, what can be said of fleet managers and admin staff that seem to have less and less time?

Organizations that can maximize time throughout their operation have a better chance at surviving slower times and will be more prosperous during busy times.
Some companies and fleet managers do not consider time to be a real cost associated with fleet maintenance. They argue that they are already paying for their staff’s time, and if it takes longer to manage a task, then so be it. This strategy can hinder the flexibility of these organizations, hamper their ability to stay competitive, and limit their ability to accomplish more, in less time. Plus, with today’s demand for skilled technicians, too much overtime will send some employees packing down the road to competitors where their time is appreciated. Then more time is spent training their replacement.
Tracking and managing a fleet in accordance with DOT regulations consumes time. More time is also required to file insurance claims that often require additional detailed maintenance reports to prove due diligence, and yet more time if litigation is involved.
There is always a duplication of effort when manually tracking and managing maintenance on whiteboards, spreadsheets, and maintenance log books - still more time.
So, if you believe time is money then there must be a real cost associated with:
The time it takes to record and manage maintenance, aside from the time it takes for technicians to perform it.
Overspending on parts due to missed parts warranty: often based on days, months, or years (time).
Wasting time due to bad decisions from inconsistent, incomplete, or missing information.
How much time can you save using Fleet Harmony Inc.?
We performed a benchmark study for a company that operated a modest for-hire maintenance shop, as well as managing a small fleet of their own. The goal of the study was to determine the cost-of-time per maintenance repair work order, using their methods and comparatively using Fleet Harmony’s Cloud Maintenance Management Software.
It was agreed that several intervals of the maintenance process would be measured and used in the cost-of-time calculation.
Technician’s handwritten notes on multi- part maintenance work order forms.
Filing of maintenance work order forms.
Searching through filing cabinets after the fact.
Entry and editing of several fleet management spreadsheets for the purpose of tracking and managing maintenance records, accidents, and driver profiles.
Entry of sales invoices into SAGE accounting software from the maintenance work order forms.
Not only did the below results of the benchmark surprise them, but we also determined that 3% of all the information captured over a 1-month time span was either inconsistent or incorrect, and required additional time to fix. To give the manual process a head start, that same 3% error rate was applied to the Fleet Harmony calculation, despite the fact that the actual error rate was only 1%.
It’s worth noting that 2 of the errors discovered in the manual process were unclaimed part warranties totaling $118.00. Fleet Harmony on the other hand, automatically alerts when parts are under warranty.

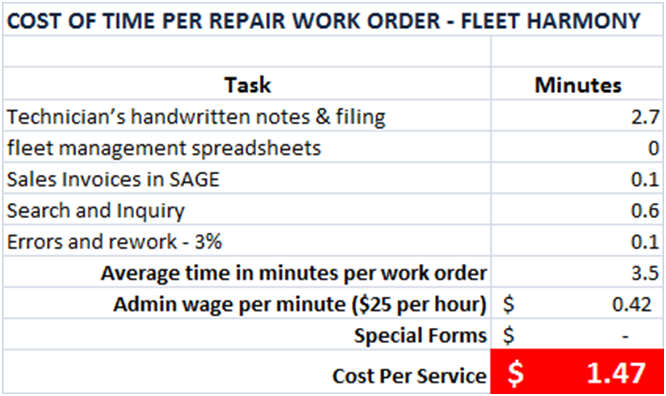
So, are you ready to stop wasting time on maintenance management, accident management, and driver profile management?
When you consider the monthly subscription price for a single unit in Fleet Harmony is less than a cup of coffee, it’s really a no brainer!
Contact Fleet Harmony Inc. to learn more.
Comments